12 Appalled Answers To Quiddity Questions About The Secrets Of Plasma Cutting
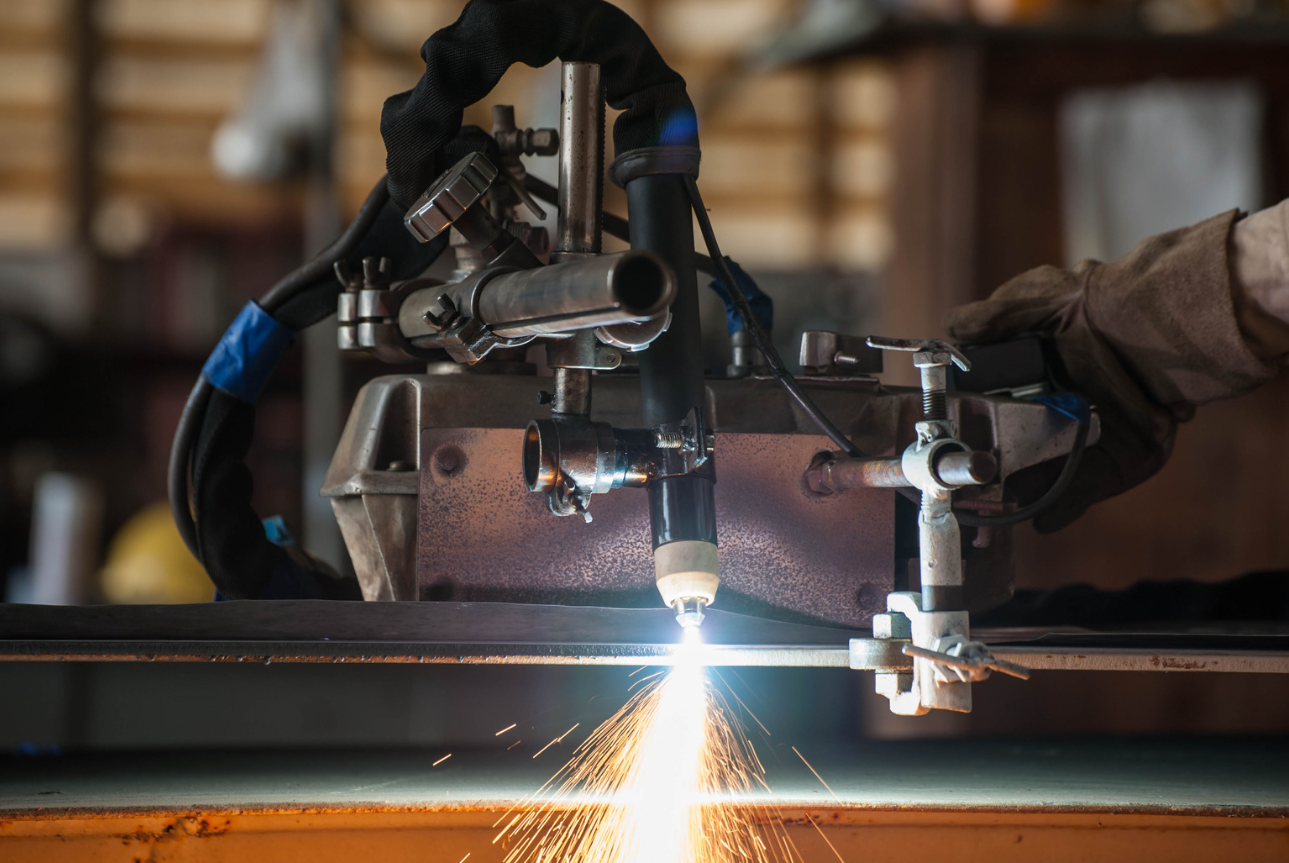
1. When was plasma cutting invented?
Plasma cutting was invented in the 1950s as a more efficient and precise method for cutting metals, particularly electrically conductive materials.
2. Who invented plasma cutting?
Plasma cutting was invented in 1955. It was developed by William Stoney Jr. and Harold Horace Baker of the engineering company, Union Carbide.
3. What does the term “plasma” mean in plasma arc cutting?
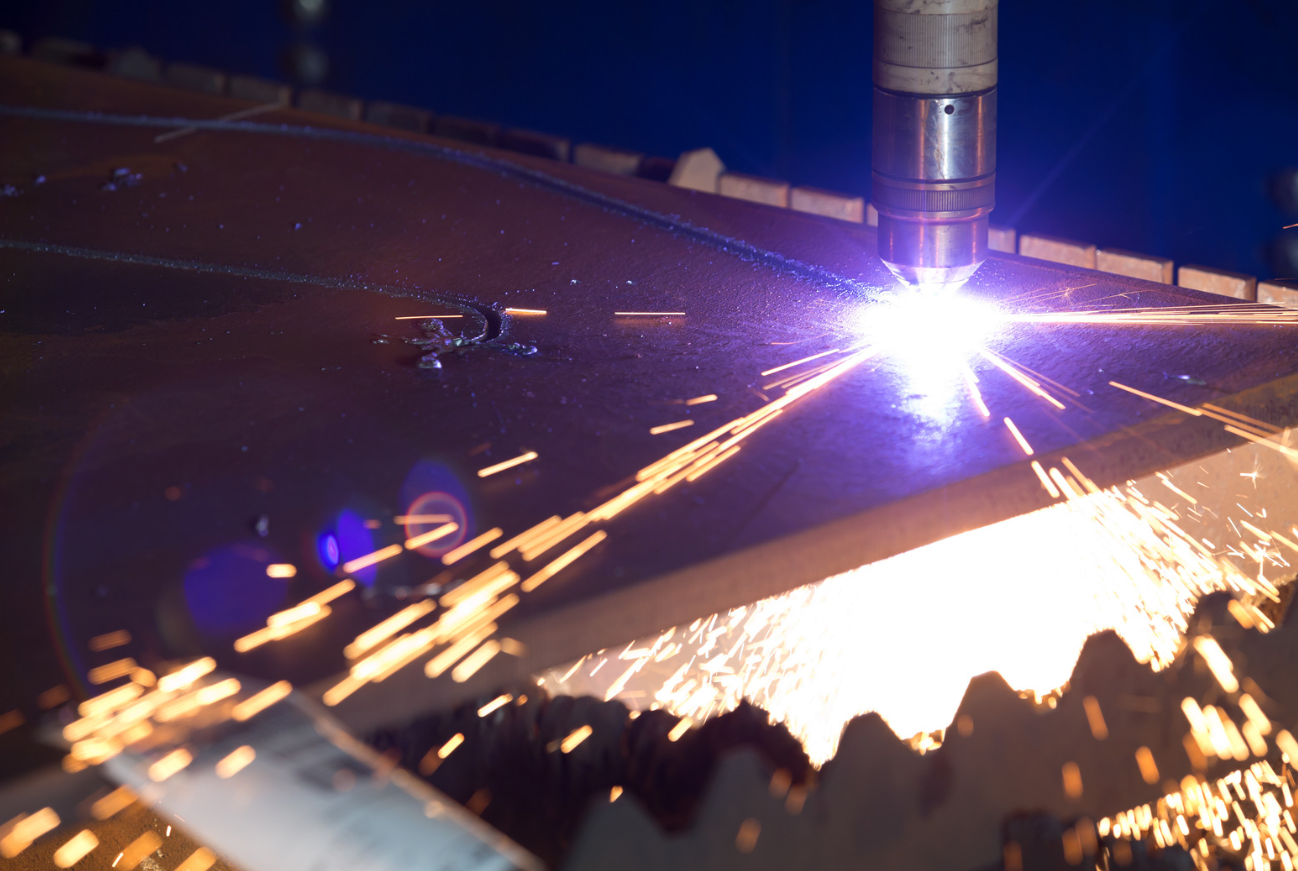
In plasma arc cutting, “plasma” refers to a high-energy, high-temperature state of gas in which electrons are separated from atomic nuclei, forming positively and negatively charged particles. Plasma arc cutting uses this high-temperature plasma gas to cut metal materials.
4. What is the hazard of plasma cutting?
Plasma cutting hazards include exposure to ultraviolet and infrared radiation, electric shock, burns from hot materials, fire risks, inhalation of toxic fumes, and noise pollution. Proper safety measures and personal protective equipment (PPE) should be used to minimize these risks.
5. How to prevent arc from plasma cutting?

To prevent the arc in plasma cutting, you can follow these steps: 1) Turn off the power source and disconnect the torch from the machine, 2) Ensure that the workpiece and cutting surface are clean and free of rust, paint, or other contaminants, 3) Use a proper grounding connection, 4) Check and maintain the proper gas flow and pressure, and 5) Inspect the torch and consumables for wear and replace them if necessary.
6. How to deal with plasma cutting fumes?
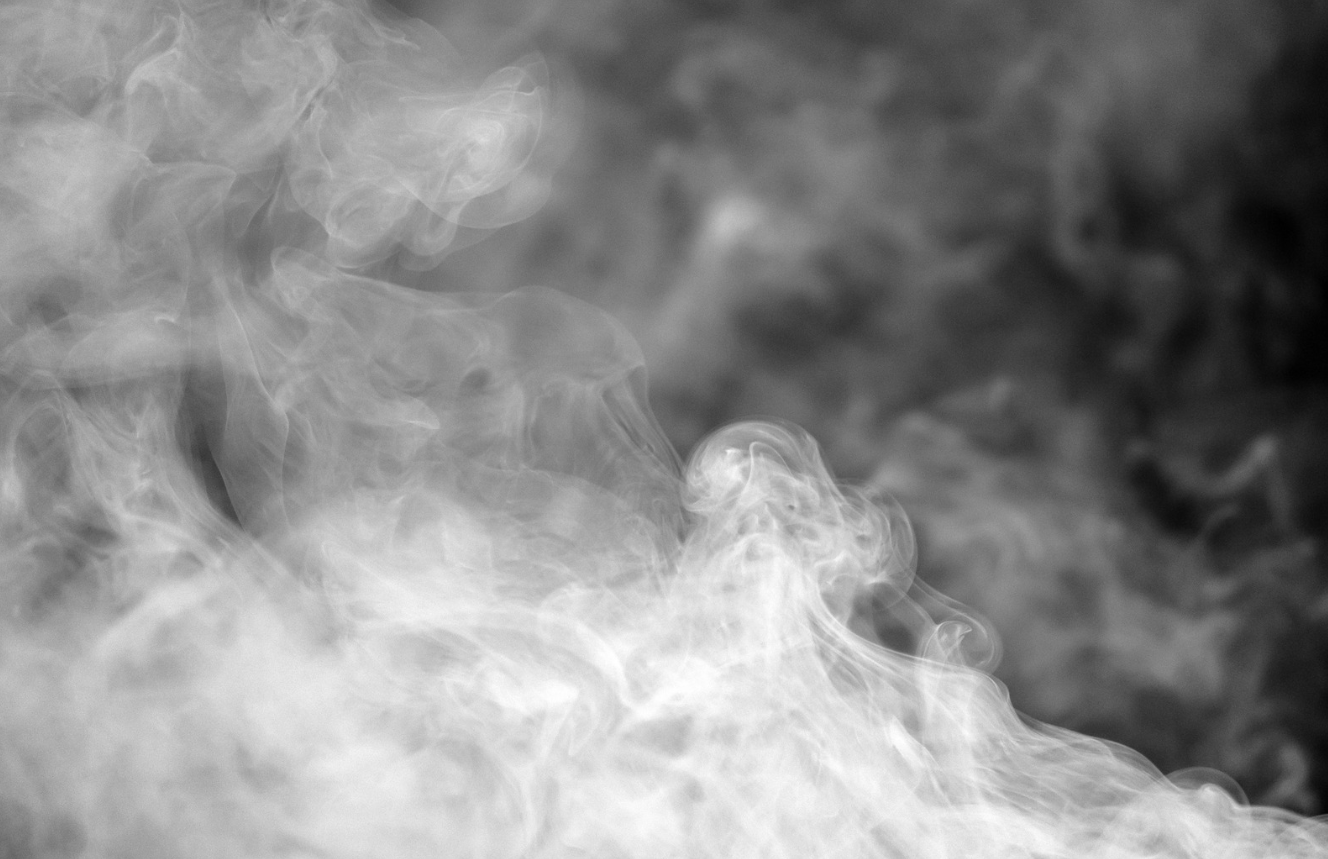
Dealing with plasma cutting fumes is essential to ensure a safe and healthy work environment. Proper ventilation, filtration, and personal protective equipment (PPE) can help mitigate risks associated with plasma cutting fumes. Here are some suggestions on how to deal with them:
1. Ventilation
Adequate ventilation is critical for removing fumes and maintaining good air quality in the workspace. Consider implementing the following:
– Local exhaust ventilation (LEV): This system captures fumes at the source, removing them from the work area before they can spread. LEV might include fume extraction torches or downdraft tables.
– General ventilation: Ensure there is sufficient air circulation throughout the workspace by using fans, open windows, or doors. This helps dilute and disperse fumes and gases.
2. Filtration
Effective filtration systems can help clean the air and remove harmful particles:
– Air cleaners: These devices filter the air by capturing particles and fumes. They can be portable or mounted on the ceiling or walls.
– Dust collectors: These systems collect dust and fumes from the cutting process and filter them out of the air. Ensure that the collector is designed for plasma cutting applications and has a high-efficiency particulate air (HEPA) filter for optimal performance.
3. Personal Protective Equipment (PPE)
To protect yourself from inhaling plasma cutting fumes, wear appropriate PPE:
– Respirators: Wear a respirator with the proper filter cartridges designed to protect against metal fumes. Ensure the respirator fits correctly and has been tested for proper seal and function.
– Welding helmets: Use a welding helmet with a built-in air filtration system to provide additional protection from fumes and particulates.
4. Work Practices
Adopt safe work practices to reduce exposure to plasma cutting fumes:
– Position yourself to avoid directly inhaling fumes.
– Keep the cutting torch at a proper distance from the workpiece to minimize fume production.
– Clean the work surface before cutting to remove any coatings or contaminants that could contribute to fume generation.
5. Training and Maintenance
Educate workers on the hazards of plasma cutting fumes and how to properly use PPE and ventilation systems. Regularly inspect and maintain equipment to ensure optimal performance and safety.
By implementing these measures, you can effectively deal with plasma cutting fumes and maintain a safe and healthy work environment.
7. What is the maximum wear depth (pit) allowed in a copper plasma cutting electrode?
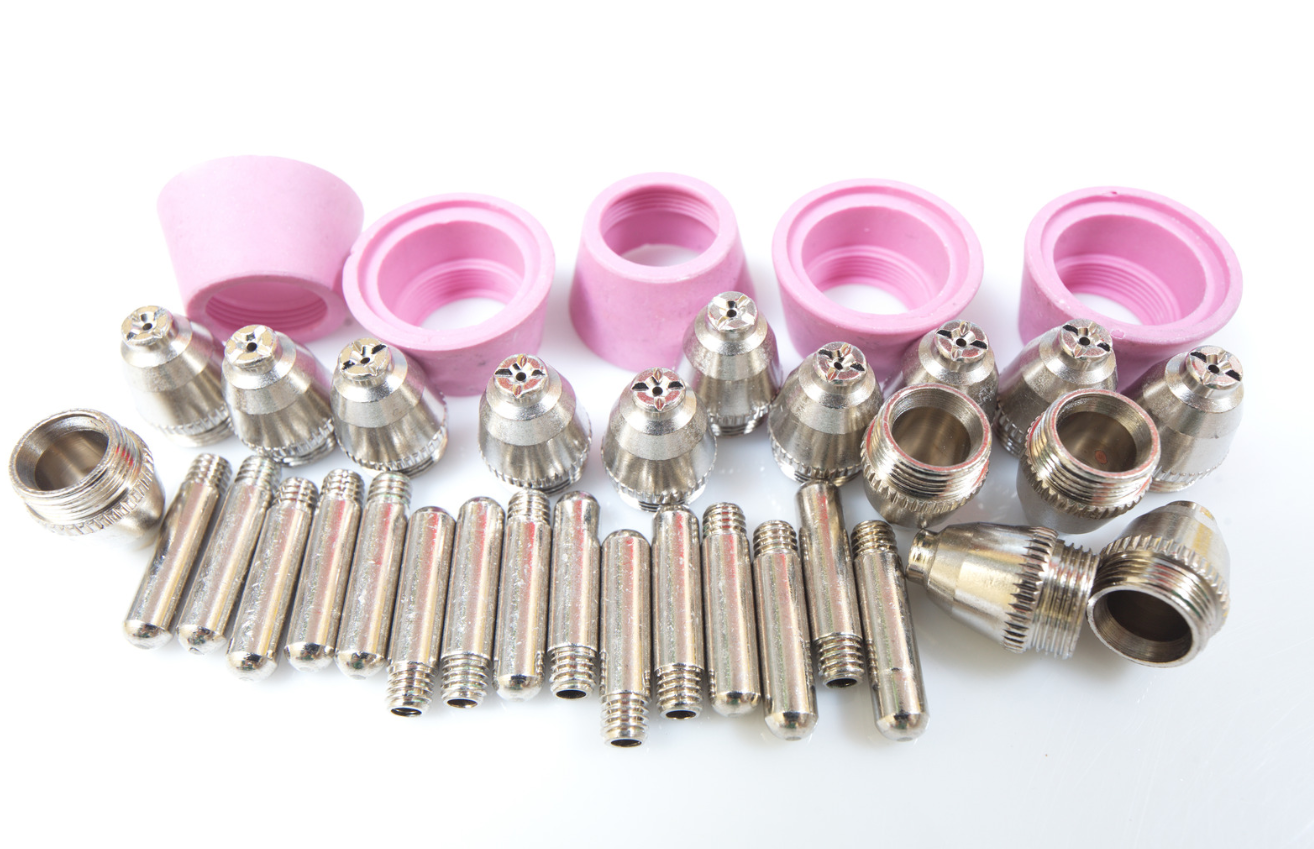
The maximum wear depth (pit) allowed in a copper plasma cutting electrode can vary depending on the manufacturer’s specifications and the specific plasma cutting system being used. As a general guideline, a pit depth of around 0.040 inches (1 mm) is often considered the maximum wear limit for many electrodes. However, it’s essential to consult the manufacturer’s guidelines for your specific plasma cutting system to determine the precise wear limits for your electrode.
Exceeding the maximum wear depth can lead to reduced cut quality, increased consumable wear, and potential damage to the torch or the system itself. Regularly inspecting and replacing worn electrodes is crucial for maintaining optimal cutting performance and prolonging the life of your plasma cutting system. Always follow the manufacturer’s recommendations for electrode inspection, maintenance, and replacement.
8. Why does my plasma torch crash into the metal when cutting?

A plasma torch crashing into the metal during cutting can be caused by several factors. Here are some common reasons and potential solutions:
1. Incorrect torch height setting (standoff distance)
The torch height, or standoff distance, should be set according to the manufacturer’s recommendations for the specific material being cut. If the torch is too close to the workpiece, it might crash into the metal during cutting.
Solution: Ensure the torch height is set correctly according to the manufacturer’s guidelines and the material being cut.
2. Malfunctioning torch height control (THC) system
If your plasma cutter is equipped with a torch height control (THC) system, it should automatically maintain the optimal standoff distance during cutting. A malfunctioning THC system can cause the torch to crash into the metal.
Solution: Inspect the THC system for any issues, such as loose connections, damaged components, or software problems. Consult the manufacturer’s troubleshooting guide or contact technical support for assistance.
3. Warped or uneven workpiece
A warped or uneven workpiece can lead to the torch coming into contact with the metal during cutting, especially when cutting thinner materials.
Solution: Inspect the workpiece for any warping or unevenness before cutting. Flatten or secure the material as necessary to ensure a smooth, even cutting surface. Adjust the torch height control system or manual torch height to accommodate any variations in workpiece thickness.
4. Worn or damaged consumables
Worn or damaged consumables, such as the electrode or nozzle, can affect the plasma arc and cutting performance, potentially causing the torch to crash into the metal.
Solution: Regularly inspect and replace worn or damaged consumables according to the manufacturer’s recommendations.
5. Incorrect cutting speed
Cutting at an incorrect speed can cause the plasma arc to lag, potentially leading to the torch crashing into the metal.
Solution: Adjust the cutting speed according to the manufacturer’s guidelines for the specific material and thickness being cut.
6. Improper setup or programming
If your plasma cutter operates with a CNC (computer numerical control) system, incorrect programming or setup parameters can cause the torch to crash into the workpiece.
Solution: Review the CNC programming and setup parameters to ensure they are correct for the material, thickness, and cutting process. Consult the manufacturer’s guidelines for proper setup and programming.
By addressing these potential issues, you can prevent your plasma torch from crashing into the metal during cutting and maintain optimal cutting performance.
9. What is Tarc in plasma cutting?
The term “Tarc” in plasma cutting might refer to a possible typo, as it is not a recognized term in the context of plasma cutting. It could be that you meant “arc,” which is a crucial element in the plasma cutting process.
The plasma arc is an electrically conductive, ionized gas created when the plasma torch applies an electrical charge to a gas (usually compressed air) passing through a small nozzle. The intense heat generated by the plasma arc (up to 40,000°F or 22,000°C) melts the metal, and the gas pressure blows away the molten material, creating a clean and precise cut.
If you were referring to a different term or concept related to plasma cutting, please provide more information or context, and I would be happy to help.
10. How often should plasma cutting fluid be changed?
Plasma cutting fluid, also known as coolant, is used in certain plasma cutting systems to cool the torch and consumables, prolonging their life, ensuring longer consumable life, and maintaining cutting performance. The plasma cutting process involves cutting electrically conductive materials using an ionized gas, and the coolant plays a crucial role in keeping the system efficient. The frequency at which the plasma cutting fluid should be changed depends on various factors, such as the type of fluid used, the cutting conditions, the material type being cut, and the manufacturer’s recommendations.
Here are some general guidelines for maintaining and changing plasma cutting fluid, incorporating the requested keywords:
- Monitor fluid condition regularly
Check the fluid condition frequently, looking for signs of contamination, such as debris, oil, or a foul odor. Contaminated fluid can reduce the cooling efficiency, leading to premature consumable wear, and potential torch damage, especially when cutting electrically conductive materials like mild steel.
- Maintain proper fluid level
Ensure the fluid level in the coolant reservoir is within the manufacturer’s recommended range, as mentioned in the operator’s manual. Insufficient fluid can reduce cooling efficiency, while overfilling can cause leaks or spills.
- Perform periodic maintenance
Some manufacturers recommend cleaning the coolant system and replacing the fluid every 6 to 12 months, depending on the system usage and cutting conditions, which can include cutting materials like mild steel or using oxy fuel cutting processes. Consult the manufacturer’s guidelines for specific maintenance intervals and procedures.
- Use the correct fluid
Always use the cutting fluid recommended by the manufacturer, as using an incorrect fluid can negatively impact the cooling efficiency and potentially damage the torch or consumables, especially when cutting electrically conductive materials.
- Follow the manufacturer’s recommendations
Different plasma cutting systems and fluids may have specific maintenance requirements. Always follow the manufacturer’s recommendations, as detailed in the operator’s manual, for maintaining and changing the plasma cutting fluid.
By regularly monitoring and maintaining the plasma cutting fluid, you can ensure optimal cooling performance, prolong the life of your consumables and torch, and maintain high-quality cuts when working with electrically conductive material and various cutting processes, such as oxy fuel cutting.
11. When was plasma arc cutting developed?
Plasma arc cutting was developed in the 1950s. The technology originated from the plasma arc welding process, which was developed by Robert Gage in 1953 at the Linde Division of Union Carbide Corporation. Recognizing the potential of the plasma arc’s intense heat for cutting purposes, researchers and engineers began to explore its application as a cutting tool.
Early plasma cutting systems were focused on cutting stainless steel and aluminum, as they offered an advantage over traditional oxyfuel cutting, which struggled with these materials. Over time, technological advancements have improved the efficiency, precision, and versatility of plasma cutting systems, making them a popular choice for cutting a wide range of metals today.
12. What is the cost of a touchmate plasma cutting machine?
Touchmate is not a recognized brand for plasma cutting machines. It is likely that there has been a mix-up with the name. If you are looking for a plasma cutting machine, there are several well-known brands and manufacturers in the industry, such as Hypertherm, Miller, Lincoln Electric, and ESAB.
The cost of a plasma cutting machine can vary significantly based on factors such as the system’s capabilities, cutting capacity, and included features. Prices can range from a few hundred dollars for entry-level, portable units to tens of thousands of dollars for industrial-grade CNC plasma cutting systems.
To find the right plasma cutting machine for your needs and budget, consider researching various brands and models, comparing features, capabilities, and prices. You can also consult with equipment suppliers or manufacturers for more information and pricing details.
Contact Us
Have any questions about plasma parts?
Plasma cutting equipment Accessories Safety protection products, etc.
Tel
+86-15370952128
lasersourcing@hotmail.com
15370952128
+86-15370952128